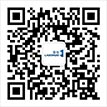
2020 官网升级中!现在您访问官网的浏览器设备分辨率宽度低于1280px请使用高分辨率宽度访问。
Lead
Xi’an Aerospace Propulsion Research Institute is a comprehensive research institute for the research, design, production and testing of liquid rocket engines for strategic and tactical missiles and large space launch vehicles in China. The unit has developed more than 100 kinds of liquid rocket engines with independent intellectual property rights, which are used in missiles, rockets, satellites and spacecraft and other fields, boosting China’s “Beidou navigation” networking, Chang’e lunar exploration, Tianwen fire detection and other major aerospace tasks.
In recent years, additive manufacturing with superior complex structure molding ability in the field of aerospace liquid power has been widely used, in order to further learn advanced additive manufacturing technology and application, to achieve “design-guided manufacturing” and “free design” and other advanced concepts, the delegation of Xi’an Aerospace Propulsion Research Institute came to Guangzhou Laseradd Technology Co., Ltd. to visit and learn.
On September 1st, a delegation of 14 people from Xi’an Aerospace Power Research Institute visited the factory of Guangzhou Laseradd Technology Co., Ltd. for investigation. Chairman Chen Bingyun, director and chief scientist Yang Yongqiang, general manager Zhang Shiqin and other leaders warmly received them.
Under the leadership of Chen Bingyun and Professor Yang, the delegation first visited Laseradd and subtractive composite manufacturing equipment, four-axis linkage CNC additive and subtractive material platform LASERADD-DED-500H, laser directed energy deposition-milling composite additive manufacturing equipment LASERADD-600. Professor Yang introduced the principle, technical characteristics and application fields of the equipment in detail. The four-axis linkage CNC additive and subtractive material platform LASERADD-DED-500H is based on directional deposition and 4-axis CNC milling processing research and development of additive and subtractive composite manufacturing processing equipment, which combines the two processing methods of traditional subtractive manufacturing and additive manufacturing, which can process metal parts with complex structures with high precision, high surface quality and high efficiency. Laser directional energy deposition-milling composite additive manufacturing equipment LASERADD-600, cradle five-axis linkage precision machining center, is a new generation of high-end five-axis equipment with three advantages of integral casting bed, moving beam Y-axis and high rigidity cradle, which can achieve high milling efficiency, high machining performance and high precision, as well as high rigidity and stability. For precision manufacturing of complex parts.
Introduction of four-axis linkage CNC additive and subtractive material platform Introduction of laser directed energy deposition-milling composite additive manufacturing equipment
The delegation was also briefed on the BJ-300 metal binder jet additive manufacturing facility launched this year. BJ-300 is a typical indirect additive manufacturing process, which has the distinctive characteristics of unsupported, large-format, high efficiency, high reliability, and compatible materials. Lei Jia independently developed the mechanical body structure of high-stability equipment, high-precision and high-efficiency powder supply structure, high-precision motion inkjet structure, and nozzle automatic cleaning structure; Support SinglePass/MultiPass bonding jet forming method, support high-speed and high-quality powder spreading, high-speed bonding forming metal powder, ceramic powder and other materials; Support ultraviolet and infrared light printing process bonding strengthening, support high-speed forming metal powder, ceramic powder and other materials; Independent research and development of data processing and integrated control software and system, convenient for operators from data processing to printing process seamlessly.
After visiting the additive and subtractive equipment, the delegation visited the production and assembly workshop of Laseradd SLM small equipment and the 3D printing and processing service department, and learned about a number of advanced main equipment of Laseradd, such as the ultra-fine SLM forming equipment DiMetal-50, which has a spot of up to 20μm; The original domestic metal 3D printing molding equipment without shielding gas DiMetal-50E; Ultra-fine shoe mold industry, special industrial metal 3D printing equipment, DiMetal-450E and other advanced equipment.
Visit the production workshop
DiMetal-50 Device Introduction
DiMetal-50E Device Introduction
Sample Visit (1)
Sample Visit (2)
Afterwards, They went to the conference room for an in-depth discussion, and Professor Yang further introduced the company’s advanced technology and product equipment to the delegation, and pointed out the development trend and research points of additive manufacturing. During the in-depth exchange, Professor Yang answered many questions from the delegation in detail and gave them new solutions to the difficult business problems they raised, such as no longer blindly pursuing high roughness requirements, but using them to design, which gave them new inspiration and thinking. The delegation said that the trip was very fruitful, enriching their understanding of the development and application of additive manufacturing technology, and helping them to optimize the design as much as possible from a practical point of view in the future.
Conference discussions