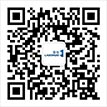
2020 官网升级中!现在您访问官网的浏览器设备分辨率宽度低于1280px请使用高分辨率宽度访问。
1. Introduction to laser selective melting and forming equipment
Selective Laser Melting (SLM) is a typical representative of modern additive manufacturing technology, and also one of the main development directions of additive manufacturing in the future. Laser selective melting technology has been widely used in aerospace, scientific research and education, medical, industrial mold, automobile and other fields because of its excellent forming precision, high density of forming parts, complex shape can be directly formed, and wide range of forming materials. The technology is mainly through laser beam is focused on the forming plane and controlled by the scanning mirror to move at a certain rate and path, the metal powder in the scanning area is quickly melted and solidified to form a solid, and finally realize the processing of complex three-dimensional structure through layer by layer accumulation.
Guangzhou Lejia Additive Technology Co., Ltd. is a high-tech enterprise specializing in the r&d, manufacturing and sales of metal 3D printing equipment and providing 3D printing services. The company team inherits the r&d experience of metal 3D printing equipment and material process from South China University of Technology for more than ten years. At present, we have launched “high precision, multi-material, large size, high efficiency” series of laser selective melting molding equipment, with years of accumulated experience in equipment stability, equipment forming ability assurance.
Usually, the laser selective melting molding equipment is mainly composed of several core parts: optical system, powder forming system, gas circulation purification system, computer control system and other auxiliary devices. The reliability and performance of each part of the molding equipment and the coordination between the parts directly affect the molding quality of the molding parts (including geometric accuracy, surface accuracy, internal defects, etc.) and molding performance (including mechanical properties, corrosion resistance, etc.), thus affecting the application of products. At the same time, the stability of the molding equipment and its continuity of work is an important guarantee for large-scale production. In the process of enterprise application, the failure of molding parts caused by equipment problems is often difficult to make up for, which not only causes the direct waste of materials, labor and other resources, but also may lead to the reduction of processing efficiency, customer loss and so on, and seriously hinder the promotion and application of technology and industrialization. Therefore, for the promotion of technology, product application, laser selective melting molding equipment to ensure the molding capacity is particularly critical.
Guangzhou Leijia additive Dimetal-100 laser selective melting molding equipment composition
2. Role and requirements of key components of equipment
(1)Optical system
As the core part of laser selective melting equipment, the optical system is mainly composed of laser, beam expanding mirror, scanning vibrator, F -θ mirror and so on. Constituency in laser melt molding process, the laser beam produced by the laser optical system and after the flexible fiber optic transmission, through the beam expander to extend the laser beam diameter, to reduce the effects on the scanning galvanometer laser energy density, finally eliminated by the f – theta lens pincushion distortion in order to get high beam quality, precise laser focal sp. The laser beam is focused on the forming surface, and under the cooperative control of the galvanometer motion control card and the computer control system, the metal powder is heated and melted at a set speed and a predetermined path, and solidifies quickly to form a solid.
In laser selective melting molding equipment, the optical system mainly has the following requirements:
(1) laser focus: through focused on the molding surface with high energy density laser beam melt metal powder, as the focus of the molding equipment from forming on the surface is too much, not only can lead to high energy density of laser beam due to lack of enough to make metal powder melting, at the same time, from large focal spot to reduce surface precision molding parts, forming limit size increases. Therefore, the focus of the molding equipment is precisely focused on the molding surface is one of the conditions to ensure the molding performance of the equipment.
2) Galvanometer calibration: Scanning galvanometer is the core component of laser selective melting molding to ensure high precision. By using the galvanometer motion control card and computer system to control the galvanometer to deflect the instruction Angle, the laser beam can scan accurately at the specified position of the forming surface. In the system, there is an inherent nonlinear mapping between the deflection Angle and plane coordinates, and the manufacturing error of optical components and the adjustment error of optical path system will bring static errors such as “pillow distortion”, “barrel distortion” and “pillow barrel composite distortion” to the system. Residual noise and analog voltage drift in electronic transmission line also bring systematic and random dynamic errors. Cumulative creep errors are often caused by temperature drift under long time continuous operating conditions. Therefore, it is very complicated and crucial to ensure the forming accuracy by galvanometer calibration.
Galvanometer system is based on the actual plane coordinate data to calculate and determine the target location and the mapping relationship between the galvanometer deflection Angle of instruction, and calibration needs to the actual processing of so plane coordinate data collection, collection of data used in the galvanometer further calculation of calibration of the control unit, so can make the galvanometer scanning precision meet the requirements. The traditional data acquisition method is manual measurement or offline automatic measurement with 3D image measuring instrument. This manual or off-line measurement method, on the one hand, will bring more subjective measurement error, on the other hand, is less efficient. Therefore, it is expected to improve the forming accuracy of laser selective melting equipment by improving galvanometer calibration technology.
Galvanometer calibration process
(3) Laser delay parameters: in the actual SLM processing process, the rotation of galvanometer motor and the output and closure of laser require a certain response time, which lags behind the system control signal, so there is a certain delay error, which has a certain impact on the molding quality of SLM parts. The bad influence of communication delay can be compensated effectively by setting the laser delay parameter in the control system. Laser Delay parameters mainly include Laser On Delay and Laser Off Delay.
For fine structure, the influence of laser delay is not negligible. Laser delay parameters have obvious effects on the density, hardness and mechanical properties of fine structures, especially on small size parts.
The effect of laser delay parameters
(4) Actual laser power guarantee: laser selection of the maximum working power of melting molding equipment will directly affect the molding capacity of the equipment, when processing metal powder with a higher melting point, often need to improve the power to ensure the complete melting of metal powder, so as to ensure the compactness and mechanical properties of the formed entity. When a certain power laser beam is emitted from the laser and absorbed or weakened by multiple optical components, the actual laser power finally reaches the forming surface will be attenuated to a certain extent. The common reason for laser power loss is that dust enters the optical path due to incorrect relative position of components or sealing problems. When the power loss exceeds a certain value, the sealing property of the optical path unit must be checked and the positions of the components on the optical path unit must be corrected until the actual measured value of the laser power reaches 90% of the theoretical value after correction.
2. Powder laying and forming system
The powder laying system of laser selective melting molding equipment mainly includes the moving mechanism of powder laying car, powder cylinder, forming cylinder and servo screw driving mechanism and other functional units. In the process of machining, forming cylinder by falling specified height, with a thick layer of powder cylinder rise a certain height (powder cylinder feeding way) or motor rotation Angle falls powder powder fell on the shop front (powder feeding way), spread powder car movement, spread powder on flexible paint shop will spread a thick layer of powder in forming cylinder surface, waiting for the optical system for processing.
In laser selective melting molding equipment, the powder paving molding system has the following requirements:
(1) Powder spreading vehicle movement mechanism: in the SLM forming process, the effect of powder spreading requires smooth, uniform and compact, which is conducive to forming dense and high surface precision parts. If the SLM forming process of powder laying plane uneven, will lead to unstable laser absorption of powder, laser irradiation on the surface of the powder bed at different positions of the power density is not equal, resulting in uneven surface forming, and finally make the forming part density, surface accuracy and other serious decline. The common problems of powdering motion mechanism are: (1) the operation is unstable, the movement of the powdering car is jitter and the stripe is formed in the powdering plane; (2) The one – way drive powder truck is prone to failure in the long running condition. Therefore, the movement mechanism of the powder laying car of the forming equipment should be easy to adjust, and the movement should be stable in the SLM forming process, and the reliability of long time operation can be guaranteed.
(2) The movement speed of the powder distributor: in the SLM forming process, properly increasing the running speed of the powder distributor can reduce the forming time of parts and improve the processing efficiency. But because the powdery structure mainly adopts the form of physical limit to control its motion range, when the pawnshop powdery car moving speed is not good, the position error caused by its acceleration or deceleration can accumulate and lead to stop, and even make parts processing failure. Therefore, the movement speed of powder dispensing car of laser selective melting molding equipment needs to be corrected and adjusted to ensure the normal operation for a long time.
(3) The movement accuracy of the forming cylinder and the powder cylinder: as a technology based on layer stacking forming, the laser selective melting molding technology has higher requirements for the movement accuracy of the forming cylinder and the powder cylinder, and the minimum layer thickness even reaches 20μm. Therefore, it is necessary to meet the motion accuracy requirements of forming cylinder and powder cylinder through system correction to ensure the forming ability of laser selective melting molding equipment.
(4) Accurate powder feeding: for the forming equipment of powder feeding mode, it takes a certain amount of time for the powder to fall from the motor to the powder trough on the car, so it is necessary to control the action time of the motor and the car to ensure that the powder falling from the motor is completely received by the powder trough. In addition, it is necessary to control the rotation momentum of the falling powder motor through testing and correction so that the falling powder can just completely cover the whole forming surface, too little powder is easy to make the forming surface part of the area can not be covered with powder, too much powder will make the powder consumption too fast.
Guangzhou Lejia Additive Dimetal-300 Multi-material laser selective melting equipment (powder feeding mode)
3. Gas circulation purification system
In laser selective melting molding process, metal powder is easy to react with oxygen or other elements in the air during laser heating and melting process, forming black smoke or high melting point spatter. On the one hand, black smoke tends to stick a layer of black smoke powder on the transparent lens, resulting in serious power attenuation when the laser passes through the lens, and the powder on the forming surface cannot be fully melted and affects the forming quality. At the same time, the lens with black smoke powder is heated due to absorption of laser energy, and even high-temperature burst; On the other hand, the high melting point spatter is easy to fall on the nearby forming area, and the subsequent laser melting will lead to inclusions and other defects. When falling on the non-forming area, it will also aggravate the pollution degree of the powder. At the same time, due to the disturbance of airflow, laser impact and powder spreading device, sealed molding room will produce a lot of dust.
Therefore, the performance of gas circulation purification system is particularly important for the molding quality control of the actual processing process. Gas circulation purification system mainly includes the following requirements:
(1) The circulating filtration and purification of the gas environment in the molding room: the protective gas entraining black smoke and splash etc. sucked from the forming surface is filtered through the filter element inside the gas circulation and purification system, and then re-used as a clean protective gas to participate in the gas circulation in the molding room. Guangzhou Lejia Additive Technology Co., Ltd. adopts a two-stage high precision filtration system, which can realize effective filtration and purification of protective gas.
(2) Tuyere design: in the molding room, the circulating protective gas mainly through the blower and suction outlet to make black smoke, splashes and other items into the circulating purification system for filtering. In the actual processing process, the circulating air field formed above the forming surface between the blower and the suction has a great influence on the forming quality of parts. The unreasonable design of tuyere easily leads to the difficulty of black smoke and splashes entering the circulating purification system for filtration in the molding room, which leads to the reduction of molding quality and the aggravation of powder pollution. Therefore, according to the actual molding environment, the structure of the blower and the suction outlet should be optimized to improve the effect of the circulating wind field on the molding surface and improve the molding quality.
(3) Optical lens protection device: in the laser selective melting device developed by Guangzhou Lejia Additive Technology Co., LTD., a second gas import is added on the basis of the traditional one gas cycle, and fresh argon gas with annular distribution is introduced under the optical lens to form a protective gas layer. Completely isolate all the combustion materials in the process of powder melting from adhering to the lens to ensure absolute laser output accuracy and greatly extend the life of optical components.
Optical lens protection device
4. Seal the molding chamber
Before SLM forming, it is usually necessary to pass inert protective gas into the forming room to remove air, so as to form an oxygen-free environment suitable for laser selective melting of powder in the forming room. If the sealing performance of the molding chamber is insufficient, it not only extends the time to exclude the air in the molding room, but also consumes more protective gas. At the same time, oxygen may enter the molding chamber and react with metal powder to generate impurities such as oxides, reducing the quality of parts forming.
Therefore, the sealing of the molding chamber is an important condition to improve production efficiency, reduce production cost and ensure the quality of parts forming. In addition, it is necessary to regularly check the sealing of the equipment and replace the sealing elements to ensure the sealing performance of the molding chamber.
5. Other
Constituency due to laser melting technology is a kind of plane based on molding and melt layer by layer accumulation of material manufacturing technology, therefore in the process of mechanical installation, forming the levelness of the plane and the levelness of the lens should be guaranteed, otherwise the parallelism of molding vibration lens surface with a plane can easily lead to huge difference between calibration of galvanometer is very difficult, Reduce molding accuracy in X/Y direction.
In addition, due to the metal powder processing, so the laser selective melting molding equipment needs regular maintenance and cleaning, in order to ensure the normal operation of each part of the equipment system, to ensure the stability of the equipment and molding ability.